QUALITY CONTROL
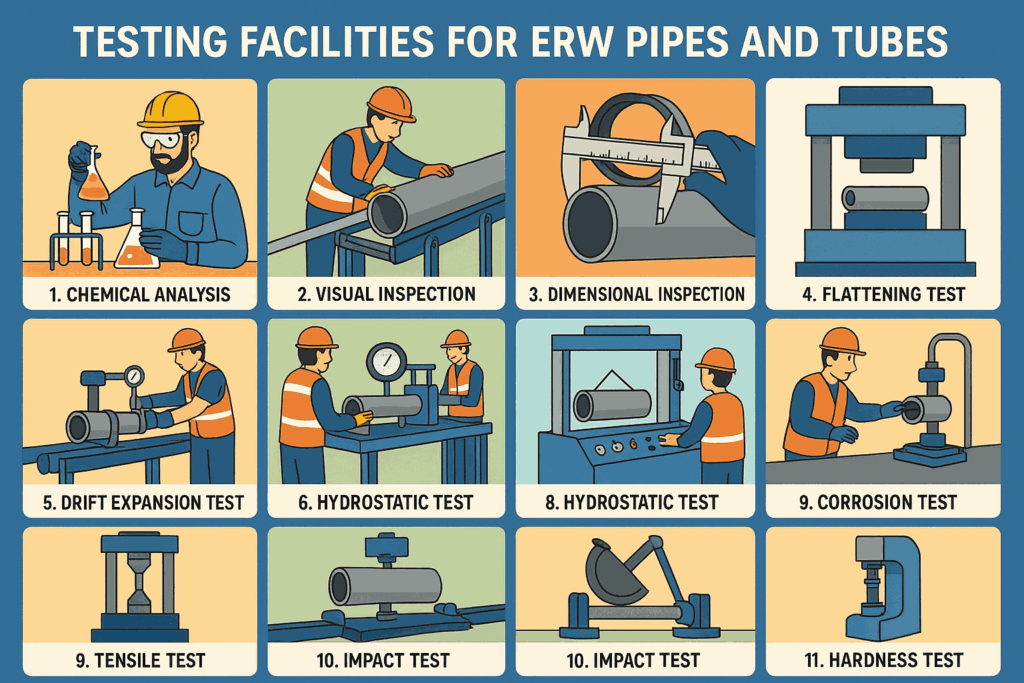
Stainless steel welded erw pipes and tubes provide high strength.
Designed to withstand pressure and tough environments.
Welded construction ensures durability.
Resists rust with grades 304 and 316.
Precision thickness ensures reliability.
Pressure-tested for safety.
Trusted in construction, engineering, and manufacturing.
Destructive TestsĀ
Test | Explanation |
---|---|
Impact Testing | Measures energy absorption at low temperatures. |
Tensile Testing (Proof Load, UTS & % Elongation) | Assesses strength and elongation under tension. |
Flattening/Reverse Flattening Test | Tests resistance to compression deformation. |
Guided Bend/Reverse Bend Test | Checks weld ductility by bending pipes. |
Flaring/Flange Test | Assesses pipe expansion and flange forming ability. |
Non-Destructive Tests
Test | Explanation |
---|---|
Chemical Testing | Analyzes chemical composition for material conformity. |
Hardness Testing (Rockwell & Superficial Scale) | Measures hardness and resistance to wear. |
Eddy Current Test | Detects surface and subsurface flaws using electromagnetic fields. |
Liquid Penetration Test | Reveals surface defects using penetrant and UV light. |
Visual & Dimensional Inspection | Inspects surface and dimensions for imperfections. |
Pneumatic Test | Checks leak-tightness by applying air pressure. |
Real-Time Radiography | Uses X-rays to detect internal defects, especially in welds. |
Automatic Visual Inspection | Conducts automated surface inspections for defects. |
Remote Visual Inspection | Uses cameras to inspect pipes in hard-to-reach areas. |
Ferrite Test | Measures ferrite content in welded areas for quality. |
Positive Material Identification (PMI) | Verifies material composition using XRF. |
Hydro Testing | Applies water pressure to check for leaks and deformations. |